來源:江南晚報
無悔過往,無懼未來。
奮斗與機遇的交鋒,格局與視野的相逢。
數字化,是一場時代的盛會。
記者走訪多家制造業企業看到,數字化轉型已經從規上標桿企業的“可選項”,成為制造業廣泛企業的“必選項”。從錫山區獲悉,該區“智改數轉”進入快進模式,最新的三年計劃中,規上企業“智改數轉”要實現全覆蓋。如火如荼的數字化浪潮開啟時代大幕,從一個個現實案例看到,疫情期間實現逆勢發展、表現足夠韌性和抗壓能力的企業,都是數字化轉型起步較早、轉型程度較高的企業,這些企業從數字平臺的構建,到新消費場景的形成,及至一個個智能車間遍地開花,克服了“不敢轉”“不愿轉”“不會轉”的重重枷鎖。
案例一
傳統企業不愿轉?
宇壽醫療:從解決痛點嘗到甜頭
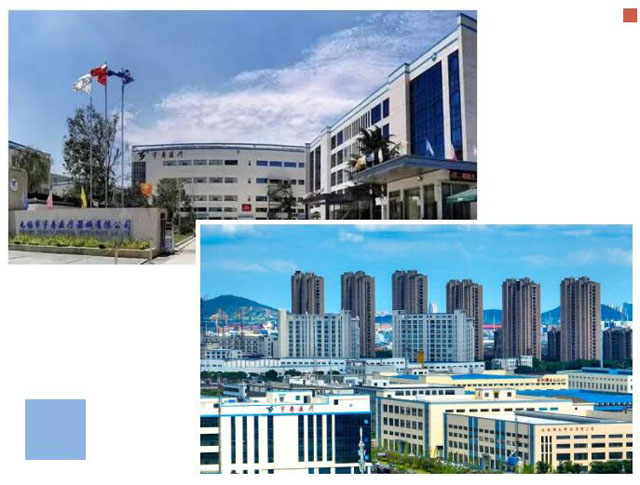
“我們生產線有個重要的工序,要把很細的金屬針頭裝到注射器上面,并進行壓力加固。因此需要大量視力特別好的員工,但頻繁的重復勞動,容易讓員工扎到自己,所以特別難招人。”
說起 2019年開始的“智改數轉”之路,宇壽醫療總經理繆李平介紹,隨著訂單量的增加,需要迅速解決產能瓶頸的“痛點”成了上馬智能化、自動化生產線的初衷。
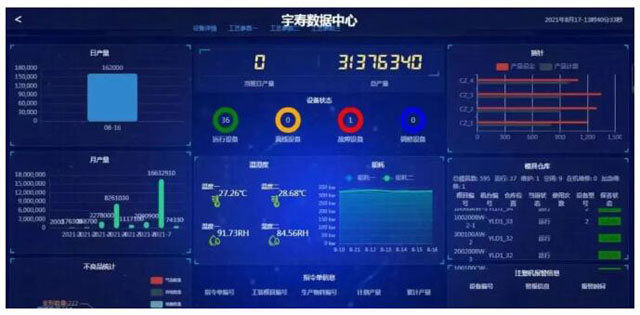
記者在宇壽醫療看到,目前公司日常的訂單排單、生產現場以及包裝發貨,均能通過智能工廠的總控平臺“一網統管”,這個智慧中樞內,統籌整個注射器、口罩等生產線的智能化、自動化運行。除了打包發貨環節尚需相對較多人工核驗,車間內僅有少量一線員工。在其自動化改造程度最大的注射器智能生產車間,由企業定制的“海康威視”快速檢測系統全新上線,針對插針作業環節需要上針、上油流程的高標準安全要求,產線內置的自動拍照和識別模塊能秒速剔除不合格的產品,改變人力檢測會疲勞、會走眼等弊端。
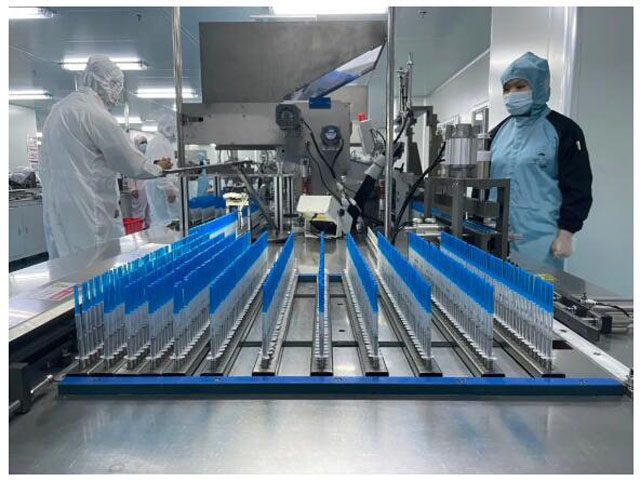
“以前最厲害的熟練工人一天能檢測1萬個針頭,而現在一套插針動作流水線上一組2人就能負責100萬支/天的產能,且產品合格率、優品率均實現了100%。”
生產現場內,穿戴防護服的工人只需關注設備運行狀態,收取剔除出的殘次品即可,而實際上幾乎沒有任何殘次品出現。據悉,這套革新后的裝配生產線投用后,連工人掉根睫毛的異常都能實時檢測出。作為國內產能最大的安全式注射器生產廠家,宇壽醫療目前單日的注射器產能可達500萬支/天,實際滿產達產僅需一線員工35人。
截至目前,
今年該企業累計已經生產
1億支以上的安全式注射器,
成為當今全球產能居前列、
國內供應量最大的疫苗注射器供應商。
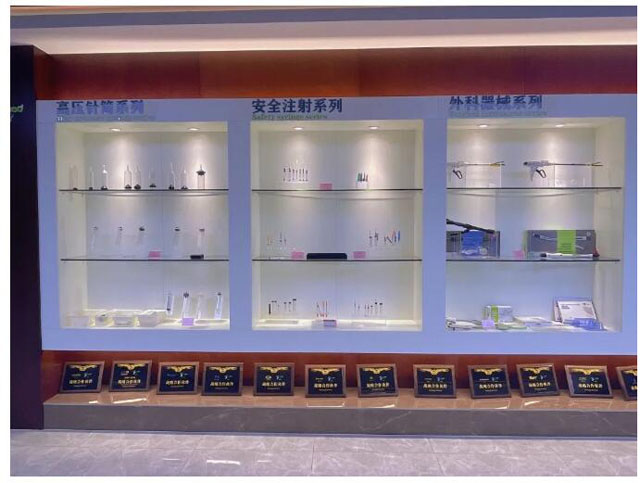
對于傳統企業來說,企業要實現生產流程的全程自動化、智能化,需要花費重資進行全新的生產路線圖設計,需要根據自己的需求和習慣重新規劃生產方式,同時也意味著整條生產線的兜底重建,一條生產線動輒數百萬元的自動化改造,“機器換人”到底值不值得?能否為企業的發展持續賦能?宇壽醫療的經驗是,值得。就在最近,這家企業獲評2022年全國第四批“專精特新”小巨人,成為國內細分領域的行業隱形冠軍。“很顯然,數字化讓我們實現了生產效率的升級換代,2019年開始企業陸續投入9000萬元進行數字化改造,其中用于信息采集類的數字化改造費用為1000萬元。2018年全年產出2.19億元,2021年的業績是2018年改造前的一倍,而人力減少了三分之一,當然,這個過程還能優化進步。”
案例二
數字化扮演什么角色?
普天鐵心:轉了以后越做越高端
線上接單、線上下料、
自動生產、自動運輸,
制造業的整個生產方式
幾乎“在云端”,
一個個變壓器鐵心產品
分明又很“接地氣”。
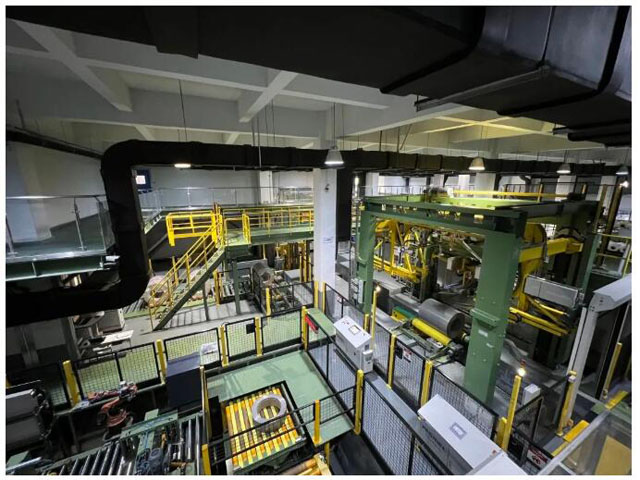
普天鐵心今年被工信部評為標桿企業數字化工廠。從一家只有十幾名工人的模仿式作業小作坊開始,位于錫山區錫北鎮的“普天鐵心”經過多年的自我創新及生產線的迭代改造,蝶變為國內全套變壓器疊鐵芯全自動智能制造工廠的新標桿。這家企業先后獲得了中國制造業隱形冠軍、江蘇省智能示范車間和智能示范工廠等榮譽,是《電力變壓器用電工鋼鐵心》國家標準的第一起草單位,在其被譽為業內“黑燈工廠”的二期智慧工廠,人均產值突破了1000萬元。

“疫情期間,全自動生產車間產能完全不受影響,管理人員即便封控在家,也能通過自主開發的綜合信息管理平臺、設備管理系統、星際物流系統等,實時獲悉、控制生產線工作狀態。”
企業副董事長梁林秋介紹,企業智能車間可智能分選并自動定時、定量配送到縱剪、橫剪及包裝設備上,整個生產、管理、供應鏈高度信息化、自動化、精益化,擁有完善的自我決策能力,在同行參觀者看來,已然是實現生產全流程自動化的“夢工廠”。
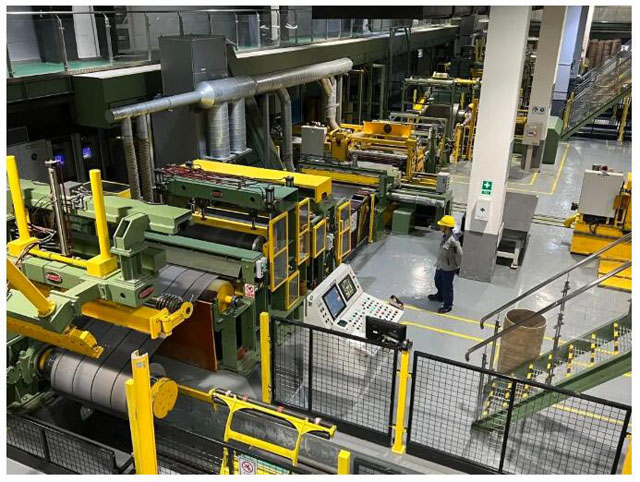
在2018年布局新建的普天鐵心二期工廠,來自瑞士的縱剪機組、德國的傳輸軌道、芬蘭的自動包裝機組,組合為同一個車間的伙伴,當系統接到訂單后瞬間生成生產指令,只見機械臂從一面重達5000噸的智能立庫墻上“抄”起一個23噸重的硅鋼卷,在縱剪機上完成大卷開小卷,接著按照薄度、規格要求將硅鋼放到作業區自主行進,然后進行剪切、套疊,實現所有生產工藝流程的最優化。整個車間內恒溫恒濕,人與人、人與設備、設備與系統之間形成一個精密的集成互聯系統,使復雜工藝在不同工序間能夠無縫銜接。
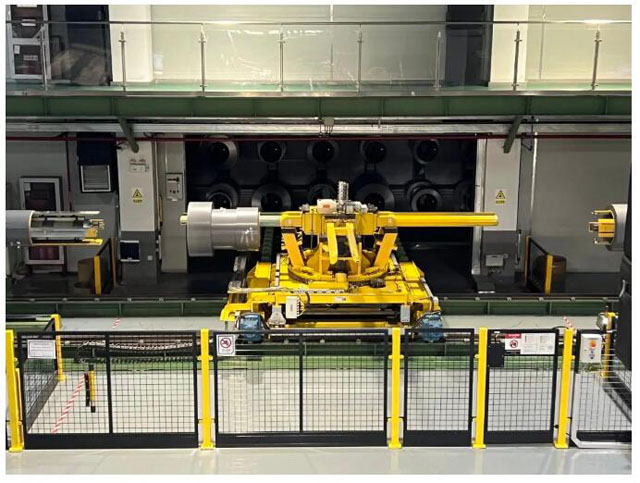
數字化在制造業究竟扮演了什么角色?
普天鐵心的答案是生產全生命周期的數據化,
從而實現系統間的深度融合。
“將運輸系統、刀具系統、生產協同系統、營銷接單系統等不同運作邏輯、不同作用的設備連接在同一個云端,形成上下游的生產順序,將采購自全球的不同機器聽從一個大腦指揮。”借助數字化,企業實現了復雜非標定制件的精細化生產,實現行業內最高標準的加工精度,且2021年單位產值能耗比2018年下降35%,2022年1—7月單位產值能耗比2018年下降58%。
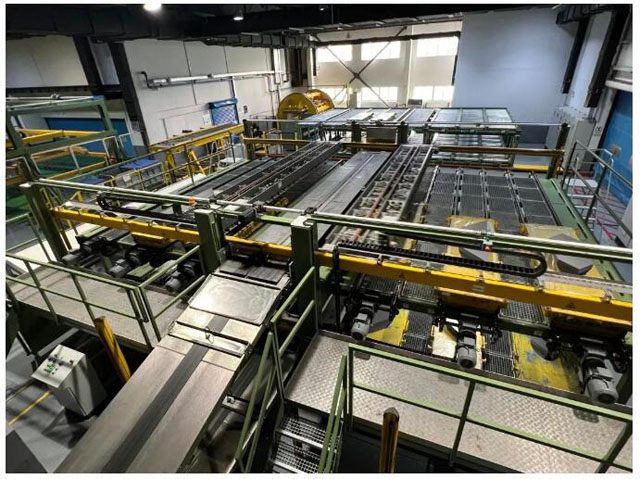
“數字化提升了企業在復雜變局下的競爭力,提高了企業產品的精度和訂單交付效率,同時更顯見的是企業應對當下以及未來的確定性。”在錫山區工信局負責人看來,普天鐵心的數字化之路,正從創新驅動的全面加速,邁向以價值為引領的高質量發展。
案例三
領先行業才能領跑賽道
紅豆工業互聯:開放平臺締造獨樂樂
到眾樂樂新生態
傳統服裝生產企業最怕什么?
庫存!
在紡織服裝生產領域深耕65年的紅豆
一直在思索為舊模式注入新活力。
2019年,
紅豆集團首次落地智能穿戴
這個新興科技領域,
摸著石頭開啟
“智能定制”的紡織業新大門。
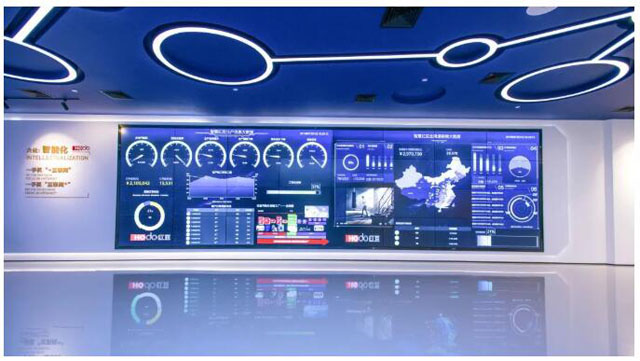
傳統的服裝生產過程是服裝公司準備面料、預測不同尺寸規格的市場份額,再進行加工生產的先生產后銷售模式,產量大意味著庫存也大的殘酷邏輯。而市場競爭激烈,產品變更頻繁,訂單趨勢越來越向多品種小批量變化,預售+生產的路徑,能最大程度減少服裝企業的“庫存”,但需要足夠敏銳快速的市場反應和快反追單能力。紅豆工業互聯是擁抱工業互聯+智能制造藍海的先行者。2019年紅豆集團宣布成立工業互聯網公司,當年12月,紅豆男裝上線“輕定制”小程序,消費者小程序上發布需求后,經過智能量體、智能打版、數據自動分發,轉向平臺工廠生產、成衣配送等私人定制全過程。目前這樣的服裝定制成本并不高,一件高級襯衫三四百元,消費者可實現1分鐘量體、2分鐘出版、72小時內準備發貨,7天內全國必達的超前消費服務體驗。
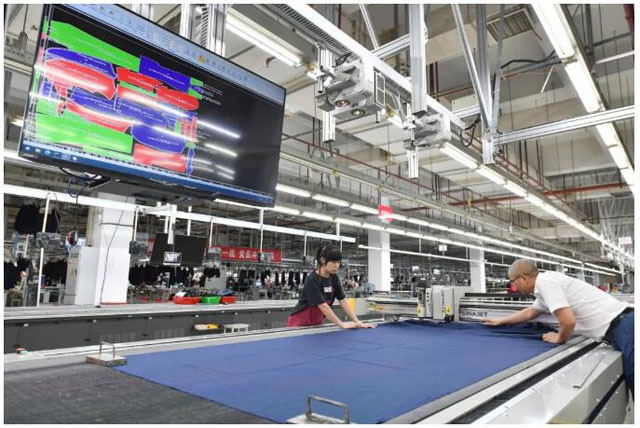
走進其中一個智能車間,每位制衣工人的工位上,都有一塊顯示屏,上面顯示每件衣服需要完成的工藝,包括每個工人當天的待完成工作量,同時對應具體的加工收入等個人工作效益。在流水線上,從前的“人找衣服”,成了“衣服找人”,自動裁床剪裁好的面料,會依次匹配給最擅長此工序的作業人員,達到在單位時間內的效能最大化。相關負責人介紹,集團內部企業打造的個性化定制+5G柔性生產智慧工廠,公司實現在制品庫存下降30%,工廠單耗成本下降10%,提高生產效率20%,實現了服裝制造鏈全過程的智能化。
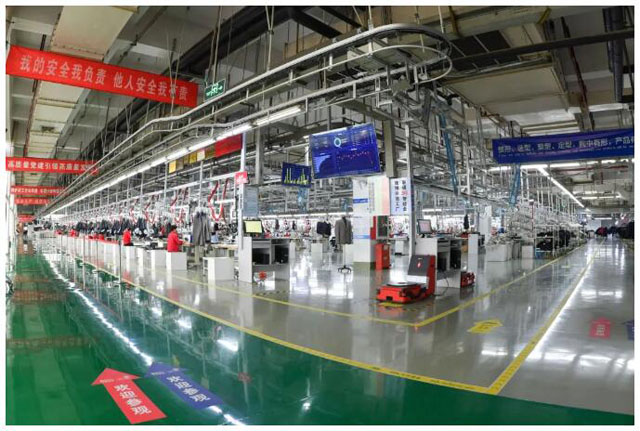
質量、成本、交期的高效協同,
進而賦予、推動整個供應鏈和
行業的技術進步、效率提升,
以及更深層次的提質增效、
整個產業鏈的協同提升。
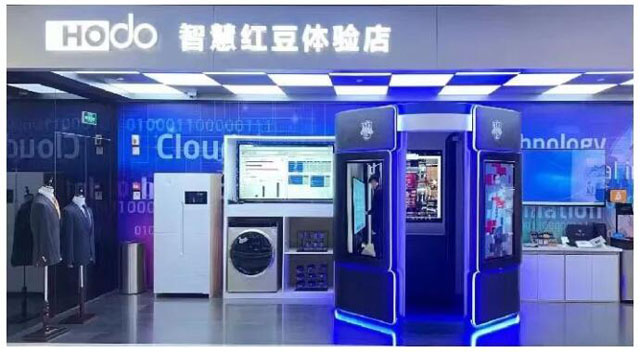
入選工信部2021年新一代信息技術與制造業融合發展試點示范項目的江蘇紅豆工業互聯實現了制造業國家“數字化”項目的突破。這個平臺,融合了紅豆居家、紅豆男裝、紅豆運動等1萬多家線下門店的消費數據集成,也上云了背后大小供應商物流、采購、銷售等現實需求的展示和進程。借助該平臺,目前已接入設備5萬臺(套),納入生態企業100家,而它采用的是免費開放給用戶和合作伙伴的模式,相關數據顯示,目前該平臺已實現交易額100億元,作為標桿型產業鏈協同生態體系解決方案,除了適用于內部300多家供應商,也向全行業10000多家企業進行推